Kokerei August Thyssen
Die Kokstrockenkühlung
Zum Inhalt:
Zur Geschichte der Kokstrockenkühlung
Planung und Lage der Kokstrockenkühlanlage
Anlagenbeschreibung
Das Kreislaufgas
Der Koksaustrag
Der Abhitzekessel
Die Koksqualität
Die Umweltschutzvorkehrungen
Die Löschwolke ist für ein jede Kokerei das Wahrzeichenhin schlechthin, denn sobald durch das Öffnen der Ofentüren der Kontakt zum Luftsauerstoff erfolgt,
beginnt der Koks bei den noch herrschenden Temperaturen zu verbrennen. Um dies zu verhindern, muß er schnell gelöscht werden. Dies geschieht in den meisten
Fällen durch das Naßlöschen (Koksnaßkühlung).
Aber es gibt noch ein anderes Verfahren des Kokslöschens. Dieses Verfahren der Wärmerückgewinnung aus dem glühenden Koks wurde fast zwei
Jahrzehnte erfolgreich auf der Kokerei AT angewandt: Das Kokstrockenkühlen (KTK).
Zur Geschichte der Kokstrockenkühlung
Die Entwicklung des Energiemarktes und verschärfte Umweltschutzbestimmungen trieben die Entwicklung der Kokstrockenkühlanlagen voran, aber über
den wirtschaftlichen Aspekt dachte man schon Anfang der 20er Jahre nach, denn Dampf war ein teures Gut. Die Idee war, die Kokswärme für Kraftzwecke
nutzbar zu machen, indem Kühlgase die Wärme aufnahmen und sie an einem Abhitzekessel mittels Wärmetauscher abgaben, um dann wieder in die
Kühlanlage zurückgedrückt zu werden. Neben diesem Verfahren der Firma Sulzer, Winterthur, Schweiz, entwickelte die Firma Collin ein
ähnliches Kokstrockenkühlverfahren, eine nähere Beschreibung hierzu findet man in "Kokerei- und Teerprodukte der Steinkohle" von
Dr. A. Spilker, 1933, S. 68/69. Auch in den Kriegsjahren dachte man verstärkt darüber nach, die beim Naßlöschen verlorengehenden
Energiemengen zu nutzen, aber die Stahlzuteilungen des damaligen "Amtes für deutsche Roh- und Werkstoffe", Berlin, ließen solche Vorhaben
nicht zu, nur notwendige Reparatur- oder Erweiterungsmaßnahmen wurden genehmigt. In den folgenden Jahren verhinderte zumindest in der BRD
die Energiepreisentwicklung ein weiteres Interesse an der Kokstrockenkühlung. Auch die Firma Sulzer stellte den Bau von KTK Mitte der 50er Jahre ein.
In den 60er Jahren begann man in der damaligen Sowjetunion das KTK-Verfahren nach Sulzer weiterzuentwickeln. Auslöser hierzu war die Eisbildung beim
Naßlöschen aufgrund der widrigen Bedingungen des borealen Klimas, das Kusnezker Gebiet, und des winterkalten Steppenklimas, der Industrieregion
des Donezbeckens war. In Deutschland waren sich zu diesem Zeitpunkt die Fachleute der Kokereiwirtschaft und die Fachleute der Anlagenhersteller noch
völlig uneinige über die Wirtschaftlichkeit der KTK-Anlagen. So schreibt Prof. Dr. Grosskinsky in seinem "Handbuch des Kokereiwesens",
Bd. I, 1955, S. 272, hierzu: " ... In vorhandenen Kokereien kann die trockene Kokskühlung kaum noch eingebaut werden, sie ließe sich deshalb
nur allmählich im verlauf von Neubauten in die Tat umsetzen. Bei Letzteren besteht die Gefahr, daß die Pioniere auf diesem Gebiet ... mit
erheblichen Verlusten rechnen müssen." Damals wie heute liegen die Kosten des Naßlöschverfahrens unter denen der Kokstrockenkühlung,
doch diese zusätzlichen Ausgaben lassen sich durch den Erlös der Energieverwertung mindern, Voraussetzung hierbei ist allerdings, daß
die betreffende Kokerei einen Käufer hat, der die Abnahme der anfallenden Dampfmenge über einen entsprechend langen Zeitraum zu einem
vernünftigen Preis garantiert.
Alle Kokstrockenkühlanlagen wie das ältere Sulzer-Verfahren und deren weiterentwickelte Verfahren (Waagner-Biró-KTK-Verfahren, Giprokoks-Verfahren)
arbeiten nach dem gleichen Prinzip der Kokstrockenkühlung im geschlossenen Kreislauf. Der glühende Koks wird in einen Kübel gedrückt,
zum Kühlbehälter transportiert, mit einem Aufzug zur Koksübergabe gehoben und dort über ein Schleusensystem in den Kühlbehälter
gegeben, der über ein Fassungsvermögen von mehreren Ofenchargen verfügt. Das Kühlgas (Kaltgas)strömt von unten mittels eines
Verteilers in den Kühlbehälter ein, durchströmt die Kokscharge, erwärmt sich dabei und wird oben abgezogen (Heißgas). Der
gekühlte Koks wird später in kleinen Mengen durch ein Schleusensystem am unteren Ende des Kühlbehälters ausgetragen. Nach
Abscheiden des mitgerissenen Koksstaubes wird das heiße Gas zum Dampferzeuger weitergeleitet. Charakteristikum des Waagner-Biró-Verfahrens ist,
daß ein teil des Kaltgases nicht in den Kübelbehälter geleitet wird, sondern direkt in den Grobabscheider. So kann durch Mischung des
Kaltgases mit dem Heißgas eine gleichbleibende Gaseintrittstemperatur im Dampferzeuger erreicht werden. Kennzeichnend für das
Giprokoks-Verfahren dagegen ist die Vorkammer mit einer Speicherkapazität von ~ 52 t/h, in der der glühende Koks nachentgast.
Auf diese Weise soll eine gleichmäßigere Koksqualität erreicht werden und das Problem der ungleichmäßigen Dampftemperatur,
-druck- und -menge beseitigt werden. Anfang der 70er Jahre interessierten sich erstmals japanische Fachleute für die in der ehemaligen Sowjetunion
weiterentwickelte Kokstrockenkühlung. Sie erwarben die Lizenzen und optimierten die Anlage indem sie u.a. eine zusätzliche Entstaubung
und bessere Gasführungssysteme hinzufügten und die Durchsatzleistung erhöhten. Auch Firmen wie Krupp-Koppes GmH, DIDIER Engieerig GmH,
D. C. Otto GmbH oder Carl Stil besh&aul;ftgten sich mit der Weiterentwicklung des Kokstrockenkühlverfahrens, denen meist das Giprokoks-Verfahren
zugrund lag.
Planung und Lage der Kokstrockenkühlanlage
Die erste für den regulären Dauerbetrieb konzipierte Kokstrockenkühlanlage in Deutschland wurde auf der Kokerei August Thyssen mit
dem Anfahren der ersten Einheit im November 1983 in Betrieb gesetzt. Im Juni 1984 folgte die Inbetriebnahme der Kokstrockenkühleinheit 2. Die
beiden KTK-Einheiten befanden sich direkt neben der Löschwagenbahn nordwestlich der Kokskohlentürme (KTKs) 1 und 2 und sind auf jeweils
70 t/h ausgelegt. Sie waren mit dem Kraftwerk Hamborn verbunden, so daß die Abnahme des Dampfes gesichert ist. Die Entscheidung für
eine Kokstrockenkühlung fiel Ende der 70er Jahre, als der Neubau der Batterie 2 notwendig wurde und mit diesem Bau umfangreiche
Umweltschutzmaßnahmen verbunden waren. Die Wahl fiel dabei auf das einzige großtechnisch bewährte Giprokoks-Verfahren,
so daß sich das Unternehmen Thyssen-Engineering um den Erwerb der Lizenzen des Unternehmens Licensingtorg bemühte. Jedoch waren
noch umfangreiche Neuerungen unter dem Aspekt Umweltschutz und Automation notwendig.
Foto-Gallerie Lightbox
Anlagenbeschreibung
Nach dem Verfahren der Kokerei AT wurde der Koks aus dem Ofen in den Kübel gedrückt, wobei der Kübel nicht verfahren wurde. Anschließend
brachte eine Lok ihn zu einer der beiden Kühleinheiten. Hier wurde er mit einem Deckel verschlossen und mittels Kran zum Übergabetrichter gehoben.
Dieser Übergabetrichter befand sich über der Vorkammer und war von dieser durch einen Beschickungsdeckel getrennt. Beim Öffnen des Schiebers
senkte sich der Kübel weiter ab und zeitgleich öffneten sich die Bodenklappen des Kübels und der Koks fiel durch den Übergabetrichter
in die Vorkammer, wobei das durch den Beschickungsvorgang verdrängte Gas hinter der Kühlkammer und vor dem Abhitzekessel dem Kreislaufgasstrom
zugesetzt wurde. Ebenso automatisch schlossen sich die Beschickungsdeckel und Bodenklappen wieder. Über den Deckel war der Kokskübel als auch
der Übergabetrichter an die Entstaubungsanlage angeschlossen. In der Vorkammer, die ein Fassungsvermögen von 250 m³ hatte, wurde die
Kokstemperatur vergleichmäßigt und der Koks zwischengespeichert, so daß er gleichmäßig der Kühlkammer zugeführt
werden konnte. Spezielle Meßeinrichtungen verhinderten ein Über- und Unterschreiten des Koksstandes. So wurde selbst bei Störungen im
Ofenbetrieb die Dampferzeugung nicht in Mitleidenschaft gezogen. Der zylindrische Kühlschacht mit 350 m³ Volumen war im Innern mit Schamottesteinen
ausgekleidet, spezielle Stahlplatten schützten die feuerfesten Steine am Boden des Schachtes.
Das Kreislaufgas
In dem gasdichten Kühlschacht wurde von unten das Kreislaufgas über einen Verteiler eingeleitet, so daß über Drosselklappen die
Gasmenge reguliert wurde, um so eine gleichmäßige Gasverteilung in der zu kühlenden Koksschüttung zu gewährleisten. Das Gas
durchströmte im Gegenstromprinzip die Koksschüttung und erwärmte sich, wobei die gesamte Enthalpie des Heißgases sich aus der
Wärme des glühenden Kokses, der restlichen thermischen Energie des Kaltgases sowie der Wärme, die durch die exothermen Reaktionen
der Nachentgasung freigesetzt wurde, zusammensetzt. Ein kleiner teil der gesamten Enthalpie dient dabei als Reaktionswärme, da bedingt durch
die hohe Temperatur und Mangel an Sauerstoff, Kohlendioxid mit Kohlenstoff zu Kohlenmonoxid reagiert, wobei sich ein Gleichgewicht einstellt,
das Boudouard-Gleichgewicht.
Details
Die Enthalpie ist ein Maß für die Energie eines Systems, also einer räumliche Anordnung von Elementen, die eine Einheit bilden. Für die praktische Chemie spielt meist nur die Änderung der Enthalpie ΔRH, die Wärmeänderung der Stoffe bei chemischen Reaktionen, eine Rolle. Der Wert von ΔRH ist für exotherme Reaktionen negativ, da Wärme freigesetzt wird und das System somit Wärme abgibt. Für endotherme Vorgänge ist der Wert demgemäß positiv. Das tiefgestellte "R" bedeutet, daß es sich dabei um eine Enthalpieänderung bei einer chemischen Reaktion handelt.
Das Boudouard-Gleichgewicht ist das nach O. L. Boudouard benannte Gleichgewicht zwischen Kohlendioxid (CO2) und Kohlenmonoxid (CO), das sich bei der Umsetzung von Kohlendioxid mit glühendem Kohlenstoff einstellt.
CO2 + C ↔ 2 CO | Δ H = +41,2 kcal
Da diese Reaktion endotherm verläuft, liegt dieses Gleichgewicht bei höheren Temperaturen mehr auf der rechten Seite, der Produktseite. Dies gilt ebenso für den Wassergasprozeß, ab 810 °C verschiebt sich das Gleichgewicht immer stärker nach links.
H2O + C ↔ H2 + CO | Δ H = +25,4 kcal
Weiterhin kann Kohlenmonoxid mit noch vorhandenem Wasserdampf reagieren:
CO + H2O ↔ CO2 + H2 | Δ H = +9,86 kcal
Hohe Temperaturen verschieben das Gleichgewicht aufgrund der endothermen Reaktion auf die Produktseite (CO), eine Erhöhung des Drucks würde es dagegen auf die Seite der Ausgangsstoffe verschieben, da die Anzahl der gasförmigen Moleküle dadurch abnimmt.
Auf der Kokerei August Thyssen wurde die Verfahrensweise "mit Luftzufuhr" zum Kreislaufgas angewandt, eine Berührung mit dem glühenden Koks war hierbei
ausgeschlossen. Die Luft wurde in den Gassammelkanal hinter dem Kühlschacht dem Heißgas zugesetzt, so daß H2 und CO zu Wasser und Kohlendioxid
oxidieren, wobei der exotherme Charakter dieser Reaktionen zu einer leichten Erhöhung der Gastemperatur führt. Auf diese Weise wird durch
kontrolliertes Zusetzen von Luft die Gaszusammensetzung geregelt. Im Bedarfsfall wird dem Kreislaufgas Stickstoff zugesetzt. Nach Abzug des Verlustes
der im Koksstaub verblieben Wärme und der Oberflächenwärmeverluste liegt die Energieeinnahme pro t Koks bei etwa 2000 MJ.
Der Koksaustrag
Der Koks verließ mit ~ 7 % der Anfangsenthalpie den Kühlschacht über zwei Schleusen. Diese zwei Schleusen waren unter dem
Kühlschacht hintereinandergeschaltet angeordnet und durch Austragsklappen voneinander getrennt, die sich im Wechsel öffnen. Nachdem
die zweite Schleuse geleert wurde, wurde der Inhalt der ersten Schleuse in die zweite Schleuse weitergeleitet, so daß die erste wieder mit
Koks aus dem Kühlschacht beschickt werden konnte, wobei eine Schleusencharge etwa 2,3 t Koks betrug. Dieser Vorgang wiederholte sich etwa 30
mal in der Stunde. Die Regulierung der Austragsmenge erfolgte durch Änderung der Zeitabstände im Austragszyklus. Um Kühlgasverluste zu
vermeiden wurde permanent Stickstoff mit Überdruck in die erste Schleuse geleitet. Der Koks der zweiten Schleuse gelangte nun zu der Austragsrinne
und von hier über ein Transportband zur Sieberei. Die Temperatur des trockengekühlten Kokses betrug etwa 137 °C.
Der Abhitzekessel
Das Heißgas wurde oberhalb der Kühlkammer am Übergang zur Vorkammer durch Abzugsschlitze abgezogen und zu dem Abhitzekessel, der sich
neben der Kühleinheit befand, weitergeleitet. Dieser Zwei-Zug-Abhitzekessel war mit natürlichem Wasserumlauf ausgestattet, so daß
keine Umwälzpumpen nötig waren. Das Gas durchströmte zuerst den Leerzug, bevor es im zweiten Zug seine Wärme an den
Nachschaltheizflächen abgab. Die Wärme des Heißgases (Primärkreislauf) wurde an das Speisewasser (Sekundärkreislauf)
abgegeben: Es überhitzte zunächst den Naßdampf zu Heißdampf, bevor es den Verdampfer und die Vorwärmer passierte.
Das Speisewasser, das mit 113 °C in den Kessel eintrat, wurde erst im Gegenstrom-, dann im Gleichstromprinzip vorgewärmt bevor es zur
Obertrommel gelangte. Novum bei diesem Abhitzekessel war die integrierte Entstaubung. Auf diese Weise konnte der Verbindungskanal zwischen
Kühlkammer und Abhitzekessel stark verkürzt und so Wärmeverluste vermieden werden. Im ersten Zug des Kessels, der eine
besondere Geometrie aufwies, um die Strömungsgeschwindigkeit des Gases zu reduzieren und um einen hohen Staubabscheidegrad zu erreichen,
wurden 36,1 % und im zweiten Zug 17,4 % des Grobstaubes ausgetragen. Der Wirkungsgrad des Abhitzekessels betrug 85 %, der erzeugte Dampf 60
bar bei 455 °C und die Dampfausbeute 535 kg pro t Koks.
Die Koksqualität
Neben dem Wärmerückgewinnungsvorteil verbesserte sich auch die Koksqualität. Besonders auffällig war natürlich der
Feuchtegehalt: Trockengekühlter Koks brachte 50 kg weniger Wasser je Tonne Koks in den Hochofen. Dies hatte eine Steigerung der
Produktivität beim Hochofenprozeß zur Folge. Auch die Koksfestigkeit des trockengekühlten Kokses lag über den Werten
vom konventionell gelöschten Koks. Weiterhin beeinflußt die Nachentgasung eine unterschiedliche Zusammensetzung der flüchtigen
Bestandteile. Jedoch war der trockengekühlter Koks weniger grobstückiger. Mit 56 mm mittleren Durchmesser lag er deutlich unter dem
des naßgelöschte von 80 mm.
Die Umweltschutzvorkehrungen
Das Kaltgas gelangte mit einer Kesselaustrittstemperatur von 133 °C zu zwei Zyklonen, welche 39,9 % des Staubeintrags abschieden, so daß ein
Wirkungsgrad von 99,98 % erreicht. Anschließend wurde das Kreislaufgas zum Kühlschacht zurückgeleitet, wobei überschüssige
Gasmengen zum Unterfeuerungsgas beigegeben wurden. Zu den weiteren Umweltschutzmaßnahmen zählte die koksseitige Entstaubung bestehend
aus den mobilen Staubfanghauben, der Absaugung des Kokskübels sowie des Übergabetrichters, der Vorkammer, des Koksaustrags und des
Kaskadensiebs an der Austragsschleuse als auch die Absaugevorrichtungen der Koksübergabestellen. Bis auf die Haubenwagen, die an der Naßentstaubung
angeschlossen waren, waren die anderen über eine zentrale Absaugeanlage mit der stationären Entstaubungsanlage verbunden.
Diese Sekundärgase wurden in 4 Kammern mit je 320 Filterschläuche gereinigt. Die abgeschiedene Staubmenge betrug etwa 551 kg
Staub in der Stunde. Ihr war eine luftgekühlte Funkenkammer vorgeschaltet. Der Staub wurde in einem Zwischenbunker gesammelt und
anschließend mit dem Staub der Zyklone zu einem Mischer gefördert, dort mit Wasser befeuchtet und zur Sinteranlage weitergeleitet
wurde. Sämtliche Betriebsvorgänge der KTK-Anlage wurden von einer zentralen Warte überwacht und gesteuert. Alle Daten flossen
hier zusammen und wurden hier ausgewertet. Doppelt ausgelegte Rechnerstationen boten eine optimale Betriebssicherheit.
Die Kokstrockenkühlanlage der Kokerei August Thyssen hatte sich seit Inbetriebsetzung im Jahr 1983 - nach Ausführung einiger Änderungs- und
Verbesserungsarbeiten der Betriebsabläufe - bis zur ihrer Stillegung im Jahre 2002 in jeder Hinsicht bewährt und so ihre Zuverlässigkeit
unter Beweis gestellt.
Quellennachweis:
- Dr.-Ing. Bernhard Bussmann, Dr.-Ing. Klaus Hofherr, Dr.-Ing. Jürgen A. Philipp und Dr. mont. Fritz Reinitzhuber: "Die Kokstrockenkühlanlage der Kokerei August Thyssen - Umweltschutz, Energierückgewinnung, Produktverbesserung", Stahl und Eisen 105 (1985), S. 19/28
- Dr.-Ing. Bernhard Bussmann, Dr.-Ing. Klaus Hofherr, Dr.-Ing. Jürgen A. Philipp und Dr. mont. Fritz Reinitzhuber: "Neuere Ergebnisse beim Betrieb der Kokstrockenkühlanlagen der Kokerei August Thyssen", HdT Vortragsveröffentlichung H. 497, S. 10/14
- Dr. rer. Nat. H. Bertling, Dipl.-Ing. H. Baer: "Möglichkeiten der Verwertung zurückgewonnener Energie aus Kokstrockenkühlanlagen", Glückauf, 119 (1983), Nr. 24 S. 1203/09
- Dr. rer. Nat. H. Bertling, Dipl.-Ing. H. Baer: "Weiterentwicklung von Verfahren zur Kokstrockenkühlung", Glückauf, 119 (1983), Nr 13 S. 631/36#
- Dr. rer. Nat. H. Bertling, Dr.-Ing. E. Falk: "Der Einfluß der Kokstrockenkühlung auf die Qualitätsmerkmale von Koks", Glückauf-Forschungshefte 43 (1982) H. 1, S. 23/28
© Michaela Barz-Berg
Bild- und Textmaterial sind urheberrechtlich geschützt. Alle Rechte vorbehalten. Die Verwendung der Texte, Bilder oder Graphiken - auch auszugsweise - ohne Genehmigung des Webmasters ist strafbar.
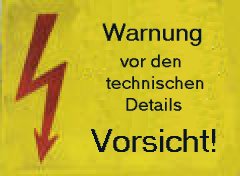
Die Enthalpie ist ein Maß für die Energie eines Systems, also einer räumliche Anordnung von Elementen, die eine Einheit bilden. Für die praktische Chemie spielt meist nur die Änderung der Enthalpie ΔRH, die Wärmeänderung der Stoffe bei chemischen Reaktionen, eine Rolle. Der Wert von ΔRH ist für exotherme Reaktionen negativ, da Wärme freigesetzt wird und das System somit Wärme abgibt. Für endotherme Vorgänge ist der Wert demgemäß positiv. Das tiefgestellte "R" bedeutet, daß es sich dabei um eine Enthalpieänderung bei einer chemischen Reaktion handelt. Das Boudouard-Gleichgewicht ist das nach O. L. Boudouard benannte Gleichgewicht zwischen Kohlendioxid (CO2) und Kohlenmonoxid (CO), das sich bei der Umsetzung von Kohlendioxid mit glühendem Kohlenstoff einstellt. CO2 + C ↔ 2 CO | Δ H = +41,2 kcal Da diese Reaktion endotherm verläuft, liegt dieses Gleichgewicht bei höheren Temperaturen mehr auf der rechten Seite, der Produktseite. Dies gilt ebenso für den Wassergasprozeß, ab 810 °C verschiebt sich das Gleichgewicht immer stärker nach links. H2O + C ↔ H2 + CO | Δ H = +25,4 kcal Weiterhin kann Kohlenmonoxid mit noch vorhandenem Wasserdampf reagieren: CO + H2O ↔ CO2 + H2 | Δ H = +9,86 kcal Hohe Temperaturen verschieben das Gleichgewicht aufgrund der endothermen Reaktion auf die Produktseite (CO), eine Erhöhung des Drucks würde es dagegen auf die Seite der Ausgangsstoffe verschieben, da die Anzahl der gasförmigen Moleküle dadurch abnimmt.